Our New Cleveland Plant via Acquisition by Lincoln Electric
The most significant factor for Lincoln Electric's acquisition of Baker Industries was the work done in Lincoln's Cleveland, Ohio facility, which specializes in large-format metal wire additive manufacturing. We now cover the full spectrum of components and processes needed to achieve repeatable, accurate, and precise 3D-printed metal components, from manufacturing our own wire, torches, materials, software, and even the completion of post-processing utilizing Baker's extensive CNC machining capabilities. The ability to accurately print a wide range of exotic materials, such as Invar, has proven to be a massive success in manufacturing several aircraft, space systems, drones, defense applications, and much more.
See our complete list of large-format 3D printing capabilities.
In addition to our large-format metal additive manufacturing capabilities in Ohio, we offer a well-rounded portfolio of post-processing and other capabilities out of our five plants in Macomb, Michigan. "We'll often send things out to the Detroit shop for finishing, drilling, [and] any [other] secondary operations needed to complete the job," says Jerry Kablak, Program Engineer at Baker. "A lot of the jobs we get today are too tricky to machine and would take several weeks to get through a typical machine shop that would work on those tough-to-machine parts," Jerry says. "By doing this, we're actually able to be friendly with our competitors, helping them machine large, 3D-printed, metal objects or be the vendor that can go after large, complex 3D structures and send them off to a machine shop to complete their job."
Best of Both Worlds: CNC Machining and Additive Manufacturing
There is a constant debate in the manufacturing world surrounding whether 3D printing will one day replace CNC machining and other traditional manufacturing methodologies as technology evolves and becomes more efficient. However, we have managed to find the perfect balance between the two technologies.
When printed parts have gone through the necessary steps to get to a near-net finish, CNC machining operations are often a quick and easy way to bring a component to its complete and final state. To learn more about how we help CNC and additive worlds collide, visit our case study on fiberglass and composite tooling.
Not every application is suitable for 3D printing, though, especially when it comes to extremely high volumes that could be accomplished more smoothly and efficiently with traditional manufacturing technologies. Below are just some of the materials and applications that we see in our everyday world.
Large-Format Metal Additive Manufacturing Materials
Steel
Commonly used in DMLS printers, this material holds similar metallurgic properties to its casted counterpart and maintains a similar chemical makeup compared to most aluminum.
Stainless Steel
As a rust-inhibitive material, stainless steel is common for automotive and aerospace applications.
Inconel
This high-strength metal is commonly used for aerospace applications due to its light weight and high-strength characteristics.
Invar
This material is our exclusive, patented metal of choice when 3D printing for many aerospace customers. "Baker also positions itself well as a provider of 3D-printed Invar components," Jerry says. "We'll print and machine components, mostly for our aerospace customers, with tricky geometries and thin, sheet-metal-like bodies."
Learn more about this proprietary material.
Benefits and Ideal Wire Additive Manufacturing Applications
Single-Piece Components
Rocket nozzles, vehicle body paneling, and engine blocks are just a few examples of components that can now be produced as a single piece instead of several parts bolted or welded together. Additive manufacturing helps to reduce the assembly time needed to make these parts. In addition, 3D printing can typically mimic or improve the strength, rigidity, and overall toughness of these parts compared to traditional manufacturing methods.
Castings vs. Large-Format Metal Additive Manufacturing
In addition to CNC machining, casting is another technology that directly competes with 3D printing. When casting, concepts, designs, and molds must be developed/created before sending the job off to a casting/forging facility, receiving the part, and finishing production with post-processing operations to get a clean finish. The number of stages in the manufacturing process is significantly reduced with additive manufacturing because everything can be printed in one run and the component often requires little to no post-processing operations.
Reduced Inventory, Faster Turnaround Times
For traditional manufacturing methods, time to market can be significant once design, setup, secondary operations, shipping, and all other small steps in-between are taken into account. With additive manufacturing, organizations can operate as demand arises, producing parts as needed and reducing the need to keep an inventory of a mass-produced item. Little or no inventory means lower overhead costs associated with warehousing and maintaining that merchandise.
More Design Freedom
It is no secret that one of the most significant advantages of 3D printing is the flexibility that a designer has when creating a concept or prototype. Variable wall thicknesses, large overhangs, and generative designs (for lightweighting applications) are among the design benefits of additive manufacturing.
Comprehensive Additive Manufacturing Solutions
With a strong portfolio of CNC machining and large-format additive manufacturing (LFAM) capabilities, we can achieve scale and advanced technologies and processes that have been unrivaled in a variety of high-mix, low-volume applications. As a result, there is rarely a job too large, small, or complex for our engineering and manufacturing team to tackle. To learn more about additive manufacturing materials, processes, equipment, and applications, get in touch with us today or check out this article.
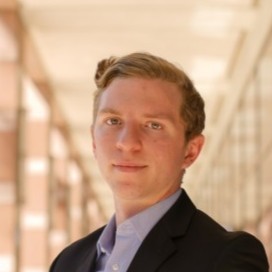