The Benefits of an Industrial Paint Booth
The new paint booth will significantly add to Baker's large-format parts' overall manufacturing process and workflow.
Interior working dimensions: 50 ft. (L) x 25 ft. (W) x 16 ft. (H)
Door opening: 22 ft. (W) x 14 ft. (H)
Consistency and Accuracy
Garmat®'s intricate filtration, temperature control, and airflow system ultimately make the painting process more repeatable and consistent. Removing debris from the outside air and maintaining a temperature-controlled environment will significantly increase consistency and accuracy.
Health and Safety
A benefit to both the employer, the employee, and governing bodies of the industrial sector is the safety the new booth provides to those who will be painting for long periods. As time has progressed, the regulations on these processes concerning employee safety have become much tighter in conjunction with emissions standards. The Garmat® systems allows any shop to comply with EPA (Environmental Protection Agency) standards as well.
Reduced Overhead, Increased Throughput
Traditional painting was previously limited by equipment and facility constraints, both of which will no longer be an obstacle with the addition of the Garmat® booth.
Garmat's Efficiency by Design
Garmat® USA equipment is built to meet or exceed all applicable codes. NFPA (33, 86, 70, 91, and 101) Standards, National Emission Standard for Hazardous Air Pollutants 6H (NESHAP subpart HHHHHH), OSHA standards (29CFR 1910.107), ETL, IFC, and IBC.
*Code compliance is dependent upon how the equipment is installed and used.
Garmat® prides itself on its intricate airflow system, which does not collect any debris or particulates from the outside world, thus maintaining the paint booth free of contaminates and protecting quality and surface finishes. "Our [booths] bring in 100% of [the] air from outside the building, keeping the spray temperature at the desired set point. [Additionally], the paint booth will recirculate the air in the bake cycle, which can reach up to 190 degrees Fahrenheit, accelerating the drying process and thus, increasing production while saving costs on the gas fuel needed by the 4M BTU burner. All Garmat® booths have an energy conservation cycle, which puts air into recirculation in the spray mode when the painter is not using spray air," explains Ken Miklos, President of Spray Booth Products, the Garmat® distributor for Baker's new booth.
"The airflow system in their particular unit will help to exhaust all of the overspray, VOC, and smells as well as speed up the drying process [and] offer [several] filters that will keep any debris from getting into the painting stream." Additionally, the Garmat® system offers a paint mix room to assist with cleaning the painters' tools, ventilate out any harmful vapors, and maintain the overall quality and health of employees.
Workflow Improvements
The most significant benefit to Baker Industries and its manufacturing offerings will be primarily from the throughput and workflow improvements seen with a new spray paint booth. "A number of some of Baker's larger aerospace jobs would take an average of three days to complete; that same set of components will now only take them a day to complete," says Miklos. "Garmat® prides itself on its relationship with distributors to be able to service all of their equipment, especially after the sale," explains Debbie Teter, Director of Sales and Marketing at Garmat® USA.
In addition to better interior lighting and an intricate filtration system, Garmat®'s industrial-grade equipment includes paint booth enclosures for automation packages, providing clean environments for those wanting to complete automated spraying at a production level. Ken Mikols, Garmat® Distributor for the Detroit area, has taken advantage of the advanced engineering in Garmat paint booths for his automotive manufacturing customers. "For some of the automotive companies we serve in the Greater Detroit area, we've done [complete] automation projects for customers wanting to have an entirely automated system of spray," says Mikols.
Full-Service Machining and Manufacturing Powerhouse
The additional paint booth serves as a big step forward for Baker Industries, expanding its overall capabilities and offerings to aerospace, automotive, space, and defense customers. In addition to its robust CNC machine shop floor and additive manufacturing facilities, the ability to paint components on the fly will allow Baker to cover the entire scope of a project, from a block of raw material to the complete, assembled, and finished part shipped to the customer.
The new paint booth is currently in production, and Baker hopes to have it operational by the end of the year.
To speak with an expert about your CNC machining, fabrication, 3D printing, or finishing needs, get in touch with us today via our website, phone at +1 (586) 286-4900, or email at info@bakerindustriesinc.com.
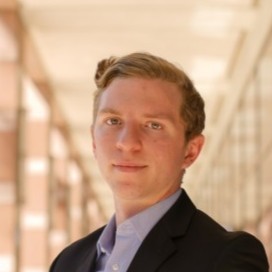