Collaborate and Educate
Baker Industries comes at a mold project from a different direction than most toolmakers might. The company involves its machinists in design up front, instead of taking the typical approach of: “Here’s the design, now figure out how to cut and build it.” Baker uses this approach even as it has added new technologies and processes to its machining operations over the years.
Macomb, Michigan-based Baker started out as a duplicating company that moved into 3D milling, five-axis machining and now additive manufacturing. Today, the company is made up of three units running as separate entities in four different facilities that service the automotive, industrial, medical and appliance industries: Baker Aerospace Tooling & Machining, Baker Machining & Mold, and Baker 3D Solutions. Plant 1 houses the company’s CNC machines, mold shop and 3D-printing lab. This lab includes two EOS M290 metal printers, and four Stratasys Fortus 900mc and one Fortus 400mc fused deposition modeling (FDM) printers (and the company is seriously considering adding some Concept Laser machines in the near future).
Baker was one of the first in its area to purchase a five-axis machine in 1998. Now, the company has 15 five-axis machines and more than 40 CNC mills. However, its philosophy is never to jump into new technology before it is ready and capable of producing products to its standard of quality. This preparedness includes having the right skilled workforce. When Baker decided to build up its compression and injection mold area, Mike Misener, director of tooling/additive manufacturing, was brought on board. His 38 years of experience in injection moldmaking and metal 3D printing has helped Baker to build molds complete with conformal cooling, and this work now drives the metal printing side of the business.
Misener says that it was demand from customers that motivated Baker to start experimenting with metal 3D printing. The company first used metal AM on fixtures that were difficult to machine, but easy to print. It outsourced this work until the company purchased its first EOS metal printer in December 2015, followed by a second EOS machine this past February. Prior to those investments, Baker had only ventured into plastic 3D printing. However, even that process had helped to revolutionize how it manufactured fixtures. For example, a typical production fixture that previously had been machined was so heavy that it took two people to handle it. Printing in plastic removed 75 percent of the weight while retaining the same required rigidity and tolerance, allowing this to become a one-person application. “With AM, if you are only thinking inside the box, you are wasting your time. You need to think outside the box and get creative,” Misener says.
Collaborative Approach
Baker’s primary focus today is on additive manufacturing and tooling, which happens to be Misener’s specialty. Earlier this year he joined forces with Excel RP/Excel Global LLC, a tooling sourcing company, to sponsor the SA Engineering Technology Center, a collaboration facility established by injection molder SA Engineering (part of SA Automotive, a Tier 1 compression molder) for emerging injection mold trends, located in Livonia, Michigan. The purpose of the center is to work with OEMs and Tier 1 suppliers to locally promote and advance R&D in new technologies for injection molding.
This center, which holds its official grand opening this month, provides a setting where reputable companies with high-level expertise in services that support injection molding can co-locate under one roof to work together to develop new technologies on 110- to 3,500-ton presses (currently Engel’s Victory 1350/285 Tech, Victory 2550/660 Tech, Duo 7050/1000 WP US, Duo 10050/1650 WP and Duo 23050/3500). This setting promotes accountability and collaborative development of repeatable processes for the new technologies, according to Misener. Through this center Baker will offer its metal 3D printing expertise and be one of several sources for any “new technology” tools.
Facility partners and sponsors include Excel RP Inc./Excel Global LLC, Engel Machinery and Trexel, along with auxiliary technology suppliers—all of which bring to the table up-to-date equipment that can help demonstrate the full potential of the new injection molding technologies. “If a tool with new technology runs at a production facility on a different machine, it may not yield the results that the SA facility demonstrated, so full testing and tryout under one roof is key,” Misener explains. This equipment is also available for purchase by customers.
New technology research being conducted at the center includes a variety of innovative molding techniques, such as Matsui RHRC, RocTool and Trexel’s MuCell. One example of the R&D underway today is rapid heat/rapid cool technology that yields high-gloss parts, which can help eliminate postprocessing. Misener believes this development could eliminate the need for paint lines at Tier 1 suppliers.
Customer Education
Baker’s expertise in building 3D-printed metal inserts with conformal cooling has helped to provide the necessary customer education and even improve some processes under testing and development at the center. For example, one customer reported problems it was having with cold spots in a heated compression mold. Baker evaluated the customer’s compression molding process and recommended conformal-cooled inserts, which would allow the mold to maintain heat more evenly. Misener says the customer was skeptical at first, because there is an ongoing misconception that adding conformal cooling requires design of a whole new tool to accommodate it.
“What they (molders) don’t realize is that they can take the traditional insert size and just change the internal geometry to get the conformal cooling they need,” he says. “You can take an existing tool with an in-and-out waterline configuration and design the internal channels without having to disrupt the entire design. You are only recreating the internal areas of the insert that are already existing in the tool. You don’t have to reinvent the wheel. Conformal cooling is a mold enhancement.” Using mold flow, cooling and warp analysis, Baker showed the customer how to implement conformal cooling in its existing tools.
Another misunderstood fact about metal 3D-printed inserts with conformal cooling is that they can be used in a production tool, if they are designed correctly. “There are wrong ways of designing conformal-cooled prototype inserts,” Misener says. He cites two common design mistakes:
- “Choking down” the insert (or quickly reducing the size of the internal chamber), which will not allow water or hot oil to flow.
- Designing a 90-degree bend in the cooling channel, which will restrict flow and “plug up” the insert. This is conventional thinking based on drilled holes and sharp bends.
Misener says both of these design mistakes negate the benefits of conformal cooling. “It is all in how you design conformal cooling with the flow of the internal channels to ensure a constant flow,” he says. “With conformal cooling, you need a flowing system, not a sharp-corner system.”
To achieve the best-case scenario with conformal cooling, Misener emphasizes the need for all the tools in the tool box, including mold flow and water flow analysis. Baker designs the conformal cooling for all of its customers, because it conducts the necessary analyses.
Looking Ahead
According to Misener, an emerging use of AM outside of conformal cooling is on gate inserts. He explains that there are a lot of conventional, off-the-shelf cashew gate and tunnel gate inserts that need to be customized, and making any modifications conventionally on a CNC machine can be difficult. Direct metal laser sintering (DMLS) allows any type of gate design or size to be placed. “We can reach any area with DMLS,” Misener says. “We grow a custom gate insert for that tool instead of modifying a shelf item. Instead of trying to make it work the best you can, DMLS can make it exactly the way you want it.”
In the end, this machining company has welcomed AM to enhance its machining operations, not replace them.
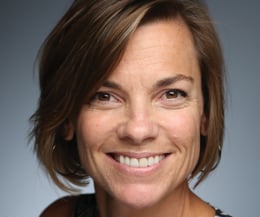