Primarily purchased for the production of large-scale frames, layup tools, bond tools, and general tooling components for customers in the aerospace and automotive sectors, the new 5-axis MECOF was installed and commissioned in December 2016. The new horizontal milling machine is the epitome of flexibility with its ability to work in both the horizontal and vertical axes with its 3+2 axis configuration that combines with a rotary table that takes the new acquisition to a 7-axis variant that allows Baker Industries to flexibly machine five sides of the workpiece in a single set-up.
The ability of the new EcoMill to conduct 5-sided machining in a single set-up will reduce the number of set-ups and secondary processes on alternate machines. For the machining of large components and tools up to 10 meters, this will significantly reduce the need for repeatedly moving parts with cranes for machining faces that cannot be processed with existing machine tools. Furthermore, the ability to complete parts in a single set-up will improve the repeatability, consistency, and overall precision of machined components. This precision is emphasized by the linear positional accuracy of P= 15+3.(L-1000)/1000µm), which equates to an ultra-precise total error of 42 microns over the complete 10-meter length of the X-axis.
Speaking to the acquisition, Scott Baker, Vice President at Michigan-based Baker Industries says: “The new EcoMill highlights our ambition to keep abreast of technology to serve our customers to the very highest of standards. The flexibility and capability of the new machine will free-up capacity on other machines in our workshop and this will enable us to reduce lead times and increase our throughput. Added to this, the 5-axis capability and dimensional capacity of the new EcoMill will give us the potential to explore more diverse types of work and industry sectors. The added capacity and flexibility positions our business particularly well for the continually changing requirements of our customer base.”
The remarkably large capacity of the EcoMill machine is highlighted by the ability to either machine jobs on the extremely spacious 10-meter travel. This unique design enables Baker Industries to process parts up to a maximum weight of 44,000 lbs. on the rotary table or a colossal 33,000 lbs./sq. ft. if parts are machined on the stationary table. In addition to the 10-meter X-axis, the EcoMill offers travel of 1300 mm in the Y-axis and 2.5 m in the Z-axis. To maximize productivity, the new EcoMill speeds around the work area with rapid travel and feed rates of 30 m/min.
Aside from the flexibility and capacity, the new EcoMill delivers an unforgiving level of rigidity and machining performance, which is ideal for the heavy-duty cutting of cast iron, steel, and aerospace-grade alloys that are particularly difficult to machine on a large scale. The heavy-duty machining potential of the new EcoMill is exemplified by the symmetrical column structure that achieves a high level of stiffness and the horizontal ram and column box-in-box design. This is complemented by a 6,000rpm 38kW spindle motor that has a torque output of 600Nm that retains exceptional power output throughout the complete speed range.
Working in synergy with the spindle motor is a CAT50 spindle taper that accommodates large cutting tools. The spindle nose is supplied tools via a 40-tool automatic tool changing system that gives Baker Industries the capacity to process a complete variety of jobs with minimal set-up time.
Alluding to why the 233 employee company has invested in one of the first next-generation EcoMill machines in the state, EMCO Mecof Chief Executive Officer, Dr. Ing. Stefan Hansch says: “Baker Industries is undoubtedly a market leader in its industry sector and the investment in the next generation EcoMill highlights the company’s ambition to invest in technology. The new EcoMill is one of the most powerful and flexible machine tools in its category and Baker Industries has realized the potential of the EcoMill to deliver improved productivity, efficiency, flexibility, and machining capability. The EcoMill installed at Baker Industries is an extremely robust package that is crammed with proven technology that includes the latest tool probing and gauging technology, a powerful Heidenhain CNC control system, and an extremely efficient chip extraction system. The EcoMill has been well received by the automotive and aerospace industries and we are excited to be working with such a prestigious manufacturer that works across both market segments.”
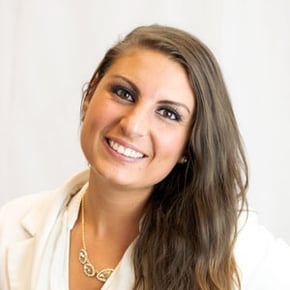